CFD simulation of SUPERCHIMNEY (atmospheric reactor)
Abstract:
The
idea of the Superchimney as an atmospheric reactor was introduced more than ten
years ago by Michael Pesochinsky. Over that time the theory explaining how the Superchimney
reactor works was introduced and small-scale testing was conducted. Despite
successful implementations, critics of the concept maintained their main
objection to the proposed model: that the reactor will not work because of
adiabatic cooling happening inside the chimney. The following study created a mathematical
model which was implemented using a CFD simulation method. The results decisively
demonstrate that the Superchimney works and no substantial adiabatic cooling
can take place inside the chimney. Moreover, if such a Superchimney were ever built
it will work and produce incredible airflows.
1- INTRODUCTION
The physical principle underlying the Superchimney is simple: Hot air rises
above cold air because hot air is less dense. Therefore, it is lighter than
cold air. In atmosphere, masses of warmer air are constantly moving up while
cooler air goes down. The chimney facilitates that upwards motion of air by
preventing the mixing of air with the colder surroundings. This stops adiabatic
cooling from happening to the parcels of air as the air is rising.
Normally, when hot air freely rises in atmosphere it expands as it gets
higher and pushes the surrounding air. That causes the surrounding air to heat
up and the rising air to cool. That process continues until equilibrium is
reached. At that point air stops its ascending.
Unlike a freely rising parcel of air, the air in the chimney is restricted
in its horizontal expansion and thus it is NOT free
rising. When air rises in the chimney it also expands, but only in the upper
direction. It compresses the layer of air above it, heats it up and loses its
own heat. At the same time the air below does the same thing. Layers of air are
being pushed and push themselves all the way to the exit of the chimney. This results
in maintaining the same amount of heat in every layer of air. This is how the
chimney works.
Notice that this explanation is different from the conventional explanation,
which refers to air draft caused by heating air inside the chimney. Unlike the
conventional explanation, the proposed mechanism states that air will flow inside
of the chimney as long as the air below is warmer than the air above. There is
no need for additional heat (like fire) to make the air move.
Now, let us consider our atmosphere. As we climb up, the temperature drops
10° C (roughly 20° F) every 1000 meters (roughly 2/3 of a mile). Let us just
assume we can build a chimney 5 kilometers (3 miles) high. Let us call it a Superchimney.
The air at the base of this Superchimney will be roughly 50°C (100°F) warmer
than at its top.
According to the Superchimney proponents air inside such a chimney
will be moving up at incredible speeds. According to the opponents the air
inside the chimney will act just as the air outside and will be cooling down,
thus reaching equilibrium and not moving up.
These studies were set up to answer that question using computational fluid
dynamics (CFD) to simulate what will happen in the chimney. As well as to
determine whether the air will move without any additional heat sources such as
green houses, fire etc.
2- Methodology: COMPUTATIONAL FLUID DYNAMICS
The simulation was conducted using Computational Fluid Dynamics
software, namely ANSYS FLUENT 19. As the work was conducted many technical
issues came up. There were limitations on the computer power available. Also,
there was lack of any other research within this field. As result certain
compromises were made:
1.
Creating
a simulation of our atmosphere proved to be impossible. The task is too complex
and involves many factors which cannot be considered by the CFD software alone.
Instead of creating a simulation of the atmosphere we created boundary
conditions which replicated our atmosphere inside the domain.
2.
The
size of the domain was limited to the bare minimum because of computational
constraints
3.
While
the results definitively answer the question of whether or not the Superchimney
will work, they cannot be used for engineering calculations because of the
multiple assumptions designed to simplify the solution. The true speeds of air
inside the chimney can be determined only when a pilot chimney is built and
physical properties are measured (air speed temperature, pressure etc). Additionally,
the studied design, which is a mere cylinder, is not the best from an air
dynamic point of view. It can be substantially improved to increase the
efficiency.
Once all geometric, meshing and
physical data were introduced into the model it was uploaded to the CFD
software in order to find a solution. All CFD software contains algorithms that
numerically solve the partial differential equations describing the movement of
any fluid, the Navier-Stokes equation.
Figure
1
: Navier-Stokes equation
This version
of the equation is called the Averaged Navier Stokes equations (RANS). It addresses
turbulent flow in a much more practical way in order to achieve a faster and
simpler resolution.
Figure 2: Reynold’s Averaged (RANS) Navier
Stokes Equations
Solving that
version of the Navier–Stokes equation produced the simulation results described
below.
3- Simulation set up, domain, boundary conditions
Numerous
research papers cover the extreme complexity of the different layers in which
atmosphere is divided as well as the multiple phenomena that take place in it.
In
addition to rising currents of hot air, lowering of the upper cold air and the
effect of the wind, there are several other phenomena which are too complex to
address through simulation. These phenomena include mesoscale and synoptic
scale structures, evolution of water vapor, influence of radiation, earth´s
Coriolis acceleration, localized breezes and other localized phenomena, etc.
In
order to accurately capture all these effects, a more evolved tool than CFD is
required. This is due to the phenomenal computing power required to analyze
them in a 3d discretized domain. All these phenomena have been excluded from
the present analysis, which intends only to demonstrate the mechanism of air
rising in a giant chimney and to prove that the adiabatic cooling phenomenon is
impossible inside a chimney. The below factors were considered and used in our
calculation:
·
Compressible behavior of air. - The
behavior of air adapts to the height or the pressure created inside the
Superchimney.
·
Solar gain on the ground due to sun
irradiation. - This is responsible for the hotter initial layers of air on the
ground.
·
Zero pressure on top of the domain in
order to simulate the end of the known atmosphere
·
Pressure gradient to the ground. - This
accounts for the static pressure present at each height level as we move away
from the ground towards upper heights.
·
Temperature gradient to the ground. - This
accounts for the lower temperature that air shows as height increases.
·
The walls of the Superchimney do not
conduct heat. - This is so that no heat exchange takes place between the
interior air and the colder exterior air.
DOMAIN
The
domain considered in the simulation consists of a square domain in which the Superchimney
is installed and has enough space around it to allow the buildup of air currents
typical for this kind of obstacle.
The
domain has a height of 10km, allowing the installation of a 5km high
Superchimney while still having enough space for the air currents above the
chimney´s exit to build properly.
The
width and depth of the domain are equal and extend 250m, forming a square in
the base. This relatively small size was chosen in order to minimize the computational
load as computing resources were limited to just one server. However, this size
is sufficient to demonstrate the mechanisms of air rising inside the chimney. The
Superchimney is 10m wide and located in the middle of the domain It is elevated
250m from the ground (so it can absorb air) and reaches a height of 5000m at
its exit.
Figure 3: Overall view of the geometry and
hexahedral mesh of the domain
TURBULENCE
MODELLING
A
2-equation turbulence model was used in order to achieve a realistic influence
of turbulence and correctly capture the boundary layer region (which however
small in size can have a significant influence on the air currents generated).
The
chosen turbulence model was K-w SST, which automatically switches between wall
functions and boundary layer calculation depending on the dimensional distance
to the wall (Y+). The main advantage of this model is that it allows use of
same first cell size all across the domain without worrying about correctly
capturing the Y+ value. This feature makes the model computationally more
expensive than the other 1 equation models such as Spalart-Allmaras.
BOUNDARY
CONDITIONS
The
boundary conditions required to reproduce the working Superchimney are
extremely complicated due to the complexity of all involved phenomena. However,
as all meso- and synoptic scales have not been included, the boundary
conditions are simplified, resulting in following setup:
Sides
and wind:
On one
side a “pressure inlet” condition was used in which the speed, temperature and
main turbulence parameters of incoming air are specified. On the opposite side
a “pressure outlet” condition was applied to allow for the air to leave the
domain.
However,
these boundary conditions may not be used with their default configuration because
they are defined as constant all across the boundary. Some additional variables
need to be introduced in order to account for the thermal and pressure
stratifications present in real atmosphere.
On both
boundaries (left and right limits of the domain) the temperature was linearly
changed from top to bottom of the boundary, starting at -70ºC at the top and finishing
at +40ºC on the bottom.
The same
strategy was used for the pressure on the right side (0 atm at the top and 1
atm at the bottom). On the left side the same pressure and temperature
distributions are used in order to account for the atmospheric gradient for
those variables.
In
order to guarantee a constant flow of air from the left to the right sides of
the domain, a 20 Pa increase was applied on the pressure distribution. This was
done in order to generate some momentum in the air and not let the numeric
residuals influence the stability of the simulations.
Top:
On top
of the domain a “pressure outlet” condition has been applied (0 atm) to allow
for air entering or exiting the domain as the simulation sees fit. This
boundary condition was used instead of installing a solid wall on top of the
domain, as that would influence the pressure distribution of the whole domain
as the simulation advances.
Bottom:
A
simple “solid wall” condition has been applied to account for the ground effect
and the effect of the sun, defining the temperature of the ground as +40ºC to
account for sun irradiation and avoid localized temperature variations on the ground.
Superchimney:
The
walls of the chimney have been defined as a solid wall with no heat conductivity.
The main purpose of this is to prevent thermal losses in the chimney and obtain
the maximum theoretical performance associated with the current design.
Initialization:
On top
of defining temperature and pressure gradients on the sides of the domain, the
simulation must be correctly initialized in order to allow the buildup of the
desired flow within the Superchimney.
Due to
the huge length of the chimney, it is suspected that it will take quite a long
time for an air draft to have enough energy to create a stream along the whole
chimney. This means that some kind of kick-start will be required. This is a
common practice when starting up hydraulic nets, pumps and other devices that
require priming.
For
this reason, the initial state from which the simulation started consisted of a
lateral air current with the corresponding thermal and pressure stratifications
(swiping from left to right of the domain) and the interior of the chimney full
of air at the maximum temperature (+40ºC). This was done to help the chimney
create the initial updraft that, later on, will be maintained by the temperature
differences in the upper and lower atmospheres.
In
order to obtain this initial flow field, a transient simulation was launched.
In this simulation the interior of the Chimney was full of hot air (+40ºC) in
order for it to start rising as soon as the simulation starts. As time in the
simulation passes, pressure, density and other variables adjust to realistic
distributions inside the chimney. This is done in a way that a user can never
describe as an initial solution for a stationary simulation.
MESH
In
order to obtain the best possible convergence of the simulation, a structured
hexahedra mesh was generated in the domain.
The
generated mesh consists of 250.000 hexahedra and, due to the simple geometry
used (square domain with a round chimney in the center), a very uniform
topology was used, keeping the skewness of all cells under 0.1 (considered
excellent mesh quality).
Figure
4
: Detail of the hexahedral mesh at the entrance (left) and exit
(right) of the chimney. Lateral view
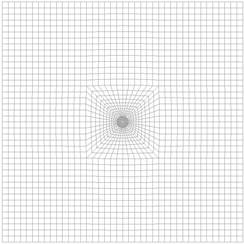
Figure
5
: Detail of the hexahedral mesh through the chimney. Top view
Results
4- STATIONARY SIMULATION
As the
first step, a stationary simulation was set up and run in order to know the
chimney works once it reaches its equilibrium state (when it is working outside
of its initial phenomena during the first minutes). The physics and boundary
conditions used are the ones already detailed in the previous chapter, except
that the simulation is launched without keeping track of time.
Once
the simulation converges, it reaches a solution and we can then observe the
pressure, speed and temperature distributions throughout the whole domain. The following
images show the distribution of these variables in different regions of the
domain.
The
most relevant parameter, due to its importance in defining the airflow, is the
pressure distribution.
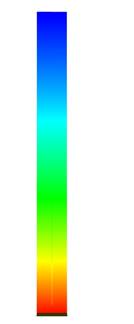
Figure
5
: Pressure field through the middle plane of the domain
On top
of the pressure gradient, between the top and bottom of the domain, the most
relevant feature detected in the pressure distribution is the difference
between pressure inside and
outside the chimney.
Pressure lowers as we move
towards the top, but the change rate is different inside the chimney, where it
gets slightly lowered more quickly on its way up. This difference in pressure
variation is associated with the lack of adiabatic cooling inside the chimney,
which accelerates the pressure reduction as we increase in height.
As a secondary
phenomenon, the pressure is also modified at the inlet and outlet regions of
the chimney. This pressure distribution is the consequence of an air stream
flowing by the inlet and outlet of the chimney, which were simulated as simple
cylindrical tubes.
These
local pressure distributions also play a role in the definitive mass flow
reached by the chimney. This is because of their strategic location right at
the entrance and exit of the chimney. In other words, the geometry of these
regions could be designed so that the pressure distribution helps the flow
inside the chimney and increases flowrate; however, this optimization has not
been explored in the current analysis as it is outside the current work scope.
Figure
7
: Pressure distribution through middle plane at the chimney inlet
region
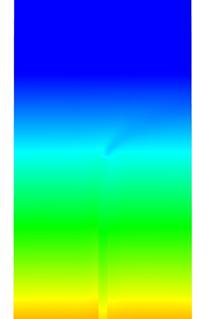
Figure
8
: Pressure distribution through middle plane at the chimney outlet
region
If we
measure the static pressure inside the chimney on its center line, we will
obtain the evolution of pressure with height. This turns out to be quite linear
when evaluated macroscopically.
Figure
9
: Pressure distribution long chimney´s centerline
The
distribution of the rest of the parameters is a direct consequence of the
pressure distribution.
The following
images show the velocity distribution in the whole domain along with a close-up
view of the entrance and exit of the chimney.
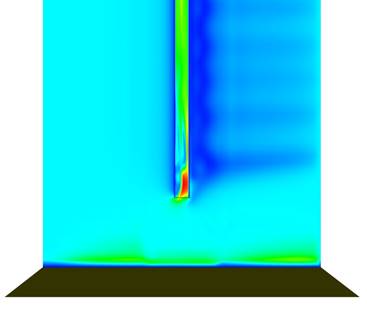
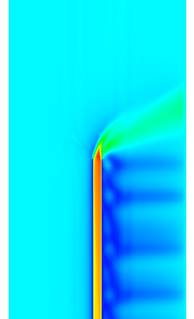
Figure
10
: Velocity distribution through middle plane at the chimney
inlet (left) and outlet (right) regions
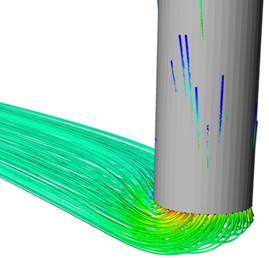
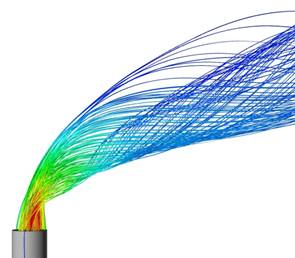
Figure
11
: Velocity flow tracks at the chimney inlet (left) and
outlet (right) regions
As was
expected, the exact velocity distribution of air as it enters or exits the
chimney is conditioned by the geometry it has to flow through. The design used
in those regions, a simple cylindrical shape, does not help increase the
flowrate in any way.
Some
improvement is expected when a more detailed design of these regions is used. They
will reduce the energy losses, thereby increasing the flowrate under the same
flow conditions.
The following
graph shows the air speed value along the chimney´s centerline. In spite of
having some local secondary flows at the inlet and outlet regions, the length
of the chimney (4.750m) makes it quite insightful.
Figure
12
: Airspeed along chimney´s centerline
The
temperature evolution responds only to the change caused by the pressure
changes because the chimney walls were defined as 0 heat conductivity.
Therefore, once the air enters the chimney its temperature remains unchanged
unless the pressure evolution causes otherwise.
The following
images show the temperature distribution in the whole domain along with a close-up
view of the entrance and exit of the chimney.

Figure
13
: Temperature distribution throughout the domain (middle
plane)
Figure
14
: Temperature distribution through middle plane at the
chimney inlet region
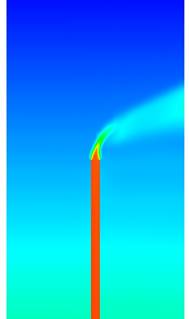
Figure
15
: Temperature distribution through middle plane at the
chimney outlet region
The following
graph shows the temperature distribution along the chimney´s centerline.
Entrance and exit regions aside, the overall temperature variation is also
quite gradual as it gains height.
Figure
16
: Temperature along chimney´s centerline
Summarizing
the results, it can be concluded that a 4.750 m chimney connecting the lower
and upper atmosphere (5 km height) does create an upward draft powered by the
lack of adiabatic cooling inside. The speed reached at the exit of the chimney
is approximately 80 m/s and its temperature has lowered around 2 ºC which is negligible.
This can be attributed to the drop of static pressure and demonstrates that
adiabatic cooling did not happen.
However,
it must be kept in mind that in order to reach this state an initial priming of
the chimney is necessary. In this case we started with a chimney full of hot
air (air at ground temperature, 40ºC). A solution that begins with an empty
chimney has not been achieved.
This
simulation does not deliver any information regarding how long it takes the
chimney to reach this state. In order to obtain more information regarding its
dynamic behavior, a transient simulation was launched with the same model.
5- TRANSIENT SIMULATION
In this
kind of analysis, a simulation is carried out which considers time and provides
a solution at every timestep. The length of the timestep, and therefore the
degree of time advance as the simulation runs, depends on many factors. The
cell size is one of the most restrictive factors. Considering how this case has
been modelled and meshed, a 0,001 timestep was eventually used, simulating a
total of 169s. It is also critical to remember that the initial state
(situation at 0 s) assumes a primed chimney (full of hot air).
Flow field
details aside, the time evolution of some main parameters (such as air speed or
temperature along the chimney) give valuable information. They show how quickly
(or slowly) the initial hot air leaves the chimney and that it starts working
by itself, powered by adiabatic expansion.
The following
graph shows the air speed inside the chimney at the outlet as time passes.
Figure
17
: Temperature evolution with time at chimney entrance and
exit
The
most relevant feature shown in this graph is the time it takes the chimney to
empty the initial hot air used to prime it. After approximately 110s the hot
air inside the chimney runs out. This shows that the reason the chimney
continues to work is NOT because of the artificially placed pocket of hot air. From
110s on the temperature of air inside the chimney stays roughly the same. The temperature
difference achieved between the entrance and exit of the chimney, once it is
working by itself, is approximately 6ºC. This can be explained by some
adiabatic cooling at the very exit of the chimney and air expansion due to the
drop of static pressure inside the chimney.
The next
graph shows the air speed at the chimney exit as time goes by.
Figure
18
: Air Speed evolution with time at chimney entrance and
exit
It can
be clearly seen that air inside the chimney accelerates as time goes by. This
implies that the buoyancy of the initial hot air is quickly surpassed by the
power of the absence of adiabatic cooling. This gradually increases airspeed as
the initial buoyancy dissipates and reaches a maximum when this initial hot air
runs out.
Care
must be taken when comparing the data from the stationary and transient
simulations, especially regarding the airspeed values. In the stationary
simulation the data was read on the centerline of the chimney, obtaining
punctual values. However, in the transient simulations an average over the
whole exit area was performed, obtaining an average value which is lower. This
is because it includes the lower speed values as we get closer to the wall of
the chimney.
Considering
all these parameters, it can be concluded that a chimney primed with air at
ground temperature would complete its start-up cycle after approximately 2
minutes. Ffrom there it sustains itself, generating a 65 m/s air current or
higher.
We
created 4 video simulations to help visualize the process of a chimney starting
with warm air inside and then running with ambient air. The simulations show
the temperature and air speed at the entrance and exit of the chimney.
Links
to Youtube:
Temperature at the
superchimney entry ---
https://youtu.be/JTDr6AN83coTemperature at the superchimney exit --- https://youtu.be/WeO-qMcvQSU
Air velocity at the superchimney entry -- https://youtu.be/N1XtPmwYtPE
Air velocity at the superchimney exit --https://youtu.be/8SMjy3jTxH8
Data
files for CFD are available upon request.
6- CONCLUSION
The
idea of the Superchimney was suggested for the purposes of energy generation,
water irrigation and, most importantly, to fight global warming. The calculations
for these processes were developed and can be reviewed on the website superchimney.org.
The present study developed the mathematical model for the SuperChimney based
on CFD methods. It proved that the Superchimney will act as a meteorological
reactor which can produce tremendous airflows. We are now one step closer to
achieving our stated goals.